AI in Production Planning: Revolutionizing Manufacturing
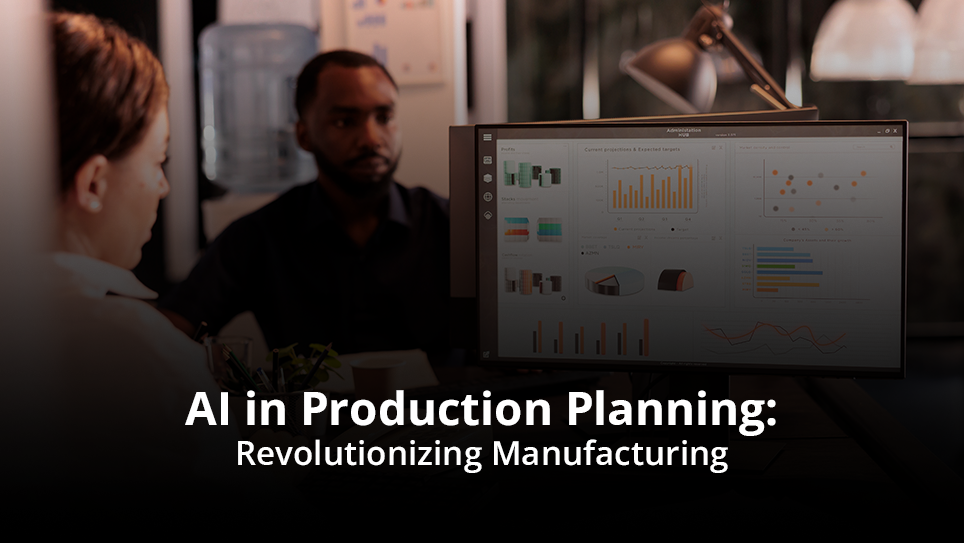
The manufacturing industry is undergoing a transformation, and at the heart of this revolution is AI in Production Planning. Gone are the days when production schedules were drawn up on whiteboards or spreadsheets based on a manager’s best guess. Today, factories are embracing advanced algorithms and machine learning models to make real-time decisions. In this new era of AI in Manufacturing, production plans are becoming more dynamic, data-driven, and efficient than ever before.
AI in Production Planning refers to the use of artificial intelligence techniques to optimize how products are made, when they are made, and what resources are used. This is not science fiction—it’s happening right now. From automotive assembly lines to electronics plants, companies are finding that Smart Manufacturing approaches powered by AI can drastically improve their agility and output. These systems analyze massive amounts of data – from supply chain information to machine performance logs – in order to fine-tune schedules and respond quickly to changes. The result? Greater manufacturing efficiency, reduced downtime, and a more resilient operation.
Decision-makers and engineering teams are taking notice of how AI can elevate production planning to new heights. In this blog, we explore the role of AI in Production Planning and how it interlinks with key aspects of modern manufacturing. We’ll dive into Smart Manufacturing, Predictive Maintenance, and AI in Supply Chain Management. Through case-style insights and practical examples, you’ll see how integrating AI into planning processes leads to significant improvements in efficiency and responsiveness. Finally, we provide actionable steps for implementing these technologies in your own operations. By the end, it will be clear why leveraging AI is not just an option but a necessity for the factory of the future.
The Role of AI in Production Planning
Production planning is the backbone of any manufacturing operation—it’s the process of determining how to produce goods in the right quantity and quality, on time, and with optimal use of resources. Traditionally, this planning relied heavily on human expertise, static rules, and historical data. The introduction of AI in Production Planning has changed the game by enabling smart, adaptive decision-making that handles complexity and uncertainty better than humans alone.
At its core, AI in Production Planning combines various AI techniques to enhance planning. For example, machine learning algorithms can forecast demand more accurately by analyzing patterns that were not evident before. With better demand predictions, manufacturers can create production schedules that closely align with actual needs, minimizing excess inventory and last-minute scrambling.
Another crucial aspect is how AI handles real-time adjustments. In a traditional setup, if a machine broke down or a rush order came in, reworking the production plan was manual and time-consuming. Now, an AI in Production Planning system can automatically recognize disruptions or new priorities and adjust the schedule on the fly.
For example, if one production line goes down unexpectedly, the AI might reschedule tasks to other lines or shifts, or suggest overtime in another area to compensate. These decisions are informed by data and algorithms that weigh trade-offs instantly. The result is a more resilient production plan that maintains output and avoids bottlenecks. In essence, AI acts as a high-speed brain for production control, reacting to changes in milliseconds—something no human planner can do alone.
Smart Manufacturing: AI Integration on the Factory Floor
In Smart Manufacturing (the cutting edge of AI in Manufacturing), the factory is fully connected and intelligent. Data flows from every machine and process (via sensors and IoT devices) into centralized systems, and AI uses this real-time information to make decisions.
For instance, if a machine begins to slow down or produces inconsistent output, the AI in Production Planning system can adjust by reassigning tasks or scheduling maintenance. With all systems interconnected, the factory operates as one cohesive, intelligent unit rather than isolated departments. This seamless integration not only boosts manufacturing efficiency by avoiding downtime, but also improves product quality by catching issues early – making AI in Production Planning a core component of Smart Manufacturing.
Predictive Maintenance: Preventing Downtime Proactively
One of the biggest threats to any production schedule is an unexpected equipment failure. A single machine breakdown can idle an entire assembly line, throwing off schedules and causing costly delays. This is where Predictive Maintenance becomes a game-changer. Predictive maintenance uses AI algorithms to analyze data from machines (vibrations, temperatures, noise levels, and error logs) to predict when equipment might fail or require service. Instead of following a fixed maintenance schedule or reacting after a breakdown, companies can service equipment right before a failure is likely to happen. This keeps machines running smoothly and aligns perfectly with the goals of AI in Production Planning.
When a company employs Predictive Maintenance strategies, the data from those systems feeds directly into production planning. Suppose sensors on a conveyor indicate that a motor is showing signs of wear and might fail in the next week. The AI planning system takes this prediction into account and schedules a maintenance window for that conveyor during a low-impact time (say, over a weekend or between production shifts).
AI in Manufacturing isn’t limited to production tasks; it extends to the upkeep of equipment itself via predictive maintenance. Many forward-thinking factories now have AI-driven systems constantly monitoring machine health. These systems use techniques like anomaly detection (spotting patterns that deviate from normal) to catch early warning signs.
For example, if a normally smooth-running machine begins to vibrate unusually, a predictive maintenance algorithm might detect this subtle change and alert the maintenance team. The beauty of this approach is that it turns maintenance into a planned part of production rather than an emergency response. Planners can even use AI tools to run “what-if” scenarios – for instance, AI in Production Planning software can simulate how taking Machine A down for two hours next Tuesday will affect the production schedule and suggest adjustments to keep orders on track.
Also read: How to Transform Your Business with Generative AI Consulting Service
AI in Supply Chain Management: Aligning Production with Demand
Manufacturing doesn’t happen in isolation. Production planning is deeply intertwined with the supply chain – it depends on the timely availability of raw materials and components, and it must respond to customer orders and market demand. That’s why AI in Supply Chain Management is a crucial companion to AI-driven production planning. When factories use AI to manage their supply chains, they gain better visibility and predictive power over supply-and-demand dynamics, which in turn makes production plans more accurate and realistic.
Inventory management is another area where AI makes a huge difference. AI in Supply Chain Management tools can optimize inventory levels by predicting lead times for supplies and detecting risks in the supply network (like a potential delay at a supplier’s plant or a transportation disruption). If an AI system flags a likely delay in a critical component’s delivery, the AI in Production Planning software can adjust the schedule preemptively – perhaps by shifting focus to other products that don’t require that component until the shipment arrives. Such agility was hard to achieve quickly with traditional planning methods.
The benefits of connecting production planning with AI-driven supply chain management are clear. First, it greatly boosts manufacturing efficiency by ensuring resources are used optimally – machines aren’t waiting idle for parts, and warehouses aren’t overstocked with excess inventory. Second, it increases responsiveness: if there’s a sudden spike in demand for a product, the system can recognize it and ramp up production (assuming the supply chain can support it). Finally, it empowers better decision-making. For instance, if data consistently shows delays from a particular supplier, managers might decide to qualify an alternate supplier or increase buffer stock. All these decisions become more data-driven and proactive thanks to AI in Supply Chain Management. By linking AI in Supply Chain Management with AI in Production Planning, manufacturing operations become much more synchronized with the real world – a hallmark of Smart Manufacturing in practice and exemplifying the broader AI in Manufacturing trend.
Real-World Scenario: AI in Production Planning in Action
Imagine a sprawling factory in Shenzhen that hums with activity despite being nearly pitch dark. In China, “dark factories” – fully autonomous production facilities – are quickly becoming a reality, running without any human workers on-site or even lights turned on. These advanced factories rely on AI-driven Production Planning as their brain, orchestrating everything from assembly lines to maintenance schedules.
It’s part of China’s aggressive push toward smart manufacturing, fueled by initiatives like Made in China 2025, which have helped the country install more than half of the world’s new industrial robots in recent years. The result is a new era of manufacturing where artificial intelligence, robotics, and IoT sensors work in unison 24/7, delivering efficiency and output at levels unattainable by traditional factories.
At the heart of each dark factory is an AI-powered production planning system that coordinates every step of the operation. This system constantly ingests real-time data: machines report their performance and health, supply chain systems feed in inventory and delivery updates, and even environmental sensors provide input. Predictive Maintenance is built into the planning – AI algorithms analyze machine data to spot signs of wear or fatigue, then automatically schedule maintenance downtime at the optimal moment before a breakdown occurs.
For instance, if a shipment of components is running late, the system will reshuffle the production sequence or redirect resources to other tasks so that no robots sit idle. Thanks to this tight integration of production planning with supply chain data and machine monitoring, the entire factory operates like a well-conducted orchestra – every robot, conveyor, and machine knows its part and timing, with the AI conductor ensuring nothing misses a beat.
Getting Started with AI in Production Planning
Implementing AI in Production Planning is a significant undertaking, but it’s a key part of any broader AI in Manufacturing strategy. Here are a few steps to get started:
- Assess Pain Points and Goals: Begin by pinpointing the biggest pain points in your production planning. Is machine downtime a frequent issue? Are demand fluctuations throwing off your schedule? Clarify what you want to achieve with AI in Production Planning – whether it’s higher manufacturing efficiency, better on-time delivery, lower costs, or all of the above.
- Invest in Data Infrastructure: AI systems thrive on data, so make sure your factory can capture and share the right information. This includes production stats, machine sensor readings, inventory levels, and quality records. High-quality, well-integrated data is the foundation of any successful AI in Production Planning initiative.
- Start with a Pilot Project: Instead of overhauling everything at once, start small. Pick a specific area to apply AI in Production Planning – for example, scheduling on one production line or deploying a Predictive Maintenance program on a critical machine – and run a pilot.
- Build Human-AI Collaboration: Train your planning team and operators to work with the AI system. The goal is synergy: humans understand and validate the AI’s recommendations, and the AI system is tuned to the realities of the factory floor.
- Scale Up, Integrate, and Stay Agile: Once the pilot proves successful, plan the rollout to broader operations. This could mean expanding AI-driven scheduling to all production lines, adding more modules (like advanced quality inspection or extended AI in Supply Chain Management capabilities), and fully embracing a Smart Manufacturing setup.
Conclusion: The Future of AI in Production Planning
The influence of AI in Production Planning on modern manufacturing is undeniable and poised to grow in the coming years. We are witnessing a shift from static, experience-based planning to more fluid, intelligent, data-driven approaches. Manufacturers that have embraced AI in Manufacturing are already seeing advantages, from more reliable production schedules and lower downtime to higher quality output and improved manufacturing efficiency. These improvements aren’t just incremental; in many cases ,they represent a step-change in performance, enabling companies to meet market demands faster and more reliably.
In conclusion, the revolution in manufacturing driven by AI is here and now, and AI in Manufacturing is becoming the new standard. AI in Production Planning is a critical piece of this transformation, enabling factories to run smarter, more efficiently, and with greater agility. By combining planning with real-time intelligence from Smart Manufacturing systems, incorporating foresight through Predictive Maintenance, and staying synchronized with market needs via AI in Supply Chain Management, manufacturers can reach unprecedented levels of performance. Those who embrace these innovations will set the pace for the industry, while those who hesitate risk being left behind. The factory of the future is not just automated – it’s intelligent, responsive, and resilient, thanks in large part to AI in Production Planning.
Want to see AI-driven production planning in action on your factory floor? FX31 Labs can help you integrate predictive maintenance, smart scheduling, and real-time supply-chain insights. Schedule a discovery call now to start maximizing uptime and manufacturing efficiency with AI.